
Your team may have experience with some of this equipment, or have contacts or resources that could help. This change is an indication of how critical maintenance is.Īsk your staff. Newer buildings are even including a formal maintenance plan with the commissioning report. Equipment lists, operating parameters, test procedures, drawings, manuals, and more could be in there as well. All the testing performed on your equipment when it was installed should be recorded in these docs. They can be a bit technical but worth looking into. If possible, look through your equipment’s commissioning reports. Does your have building have engineering or equipment documents stored somewhere? Most engineering rooms I’ve seen have a big messy file cabinet or bookshelf somewhere. Your sales rep may have this type of information available as well. Ask what they think you should check between services. If you express a genuine interest in the equipment they know so well, you may get a little tutorial. Send someone to observe, record, and ask questions next time your service rep is on-site. There is sure to be something useful out there.Īsk your service vendor or sales rep.
LOG SHEET OR LOGSHEET MANUAL
If your manual is missing, most can be found online.
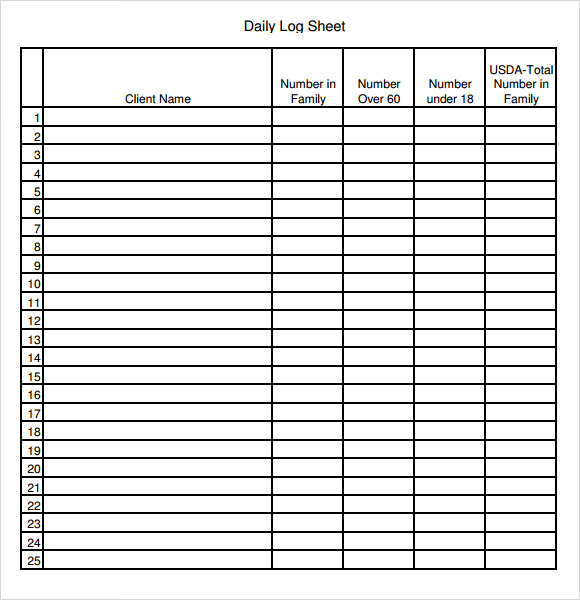
LOG SHEET OR LOGSHEET MANUALS
This might be a bit obvious, but if you can find manuals for your equipment, they should include maintenance recommendations. Unsure of how often something should be checked? Can’t remember ideal operating ranges? Here are a few ways to uncover missing information to make your schema as complete as possible:Ĭheck the manual. Having trouble filling in your schema details? Remember, you can edit any of this information later. It can take the form of an instruction, description of what to watch out for, a phone number of a vendor, a part spec, or anything else…put any relevant notes here. Explanation text – finally, this is a catch-all for anything you think might be relevant to completing this task.Minimum and maximum values – this is optional and only for items with a numerical value, but if you know the target operating range, be sure to put it in here.Frequency – how often should your team complete this check or perform this action?.Unit of measure – this can be an actual unit like °f or psi, or it can be something more general like Off, Completed, or Everything OK.Follow the examples at the top as you fill in the details for your own building.įor each Checkpoint you listed in the previous step, note all of the details you can: We created a template to help you with this part. It’s the framework of a custom maintenance manual tailored to your building. This can also be invaluable to new employees, future owner/managers, contractors, engineering, etc. Ultimately, it will help build your log sheets, but it’s an important step that lets you visualize things at a high level. Now it’s time to create what we call a “schema.” Basically, it’s just an outline of your plan. You can always go back and repeat for each location once you get up and running. Include everything, better to take it off the list later than to forget to check it.Įventually, you’ll need to do this for every Location in your building, but if that’s too much to tackle right now, start with one location and move onto the next step. IMPORTANT: Your daily maintenance routine may be significantly shorter than this initial list, so don’t hold back.
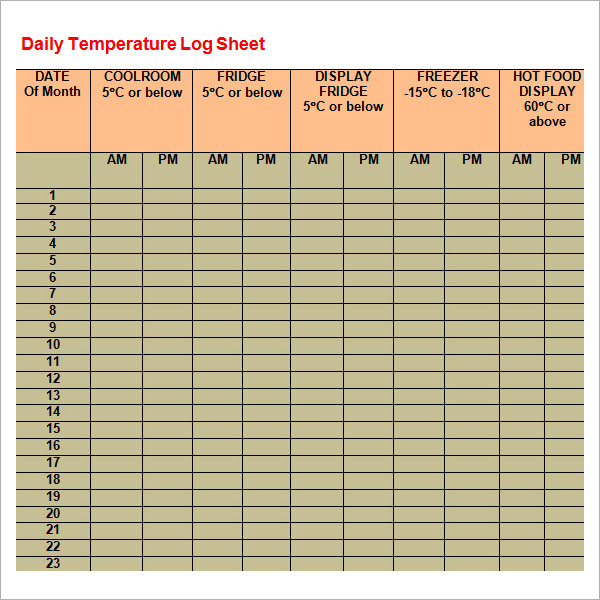
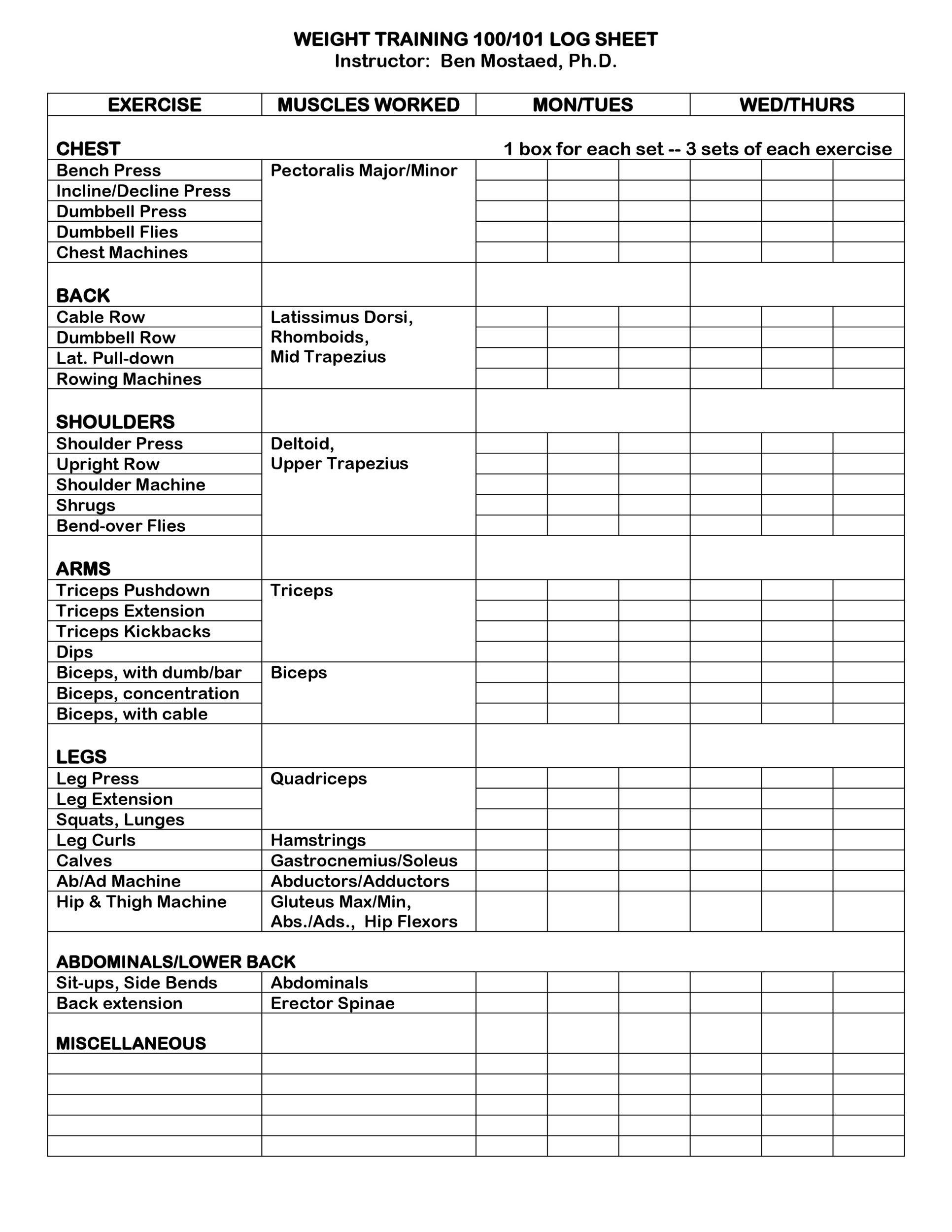
Indicate routine activities in this location as well… Visual inspection (anything to report in this room?).Here are some things you might want to check in a boiler room, for instance: But remember, it’s an iterative process and you’re taking the most important step: the first one.īefore you worry about the details, simply list out everything you can think of. This may seem daunting, and it won’t be perfect right away. Once you have your locations, indicate what needs to be checked. Or “Stairwell A – ensure stairwell is safe and clean for tenants.” List your checkpoints “Boiler room – make sure both boilers are operating safely and efficiently, and stay on top of routine maintenance. Here are some examples:įor each location, write general notes of why it’s being checked. It can be a physical location, a room in your building, or even a group of meters or a large piece of equipment. A “location” can be any place where a group of things may need to be checked.
